Like many industries, the food and beverage industry has had to contend with significant challenges since the start of the pandemic. Many of these challenges will persist post-COVID. In this article, we will explore the impact of the pandemic on SAP plant maintenance and asset management processes in the food and beverage industry. We will then discuss how to resolve many of these challenges with proven plant maintenance programs and solutions.
6 SAP Plant Maintenance Strategies
- Mobilize Maintenance to do More with Less
2. Add Automation to SAP Plant Maintenance Planning and Scheduling
3. Go Beyond Preventive Maintenance Programs
4. Structure and Capture Data
5. Attract Younger Generations to Plant Maintenance Jobs
6. Improve Operational Flexibility
Real-World Results from the World’s Largest Brewer
How Sigga Can Help
SAP Plant Maintenance Challenges Today
COVID-19 exacerbated existing challenges for the food and beverage industry and created entirely new ones. Supply Chain interruptions have stifled productivity. Plants have been forced to close following outbreaks. Wildly fluctuating consumer demand has made it difficult to optimize output.New strict safety regulations have increased costs and created logistical nightmares. And To top it all off, the labor shortage situation has become worse.
Some of these challenges will be alleviated once the world emerges from the pandemic. Others are likely to persist for generations, exacerbating pre-pandemic industry trends and further accelerating the industry’s drive towards digital transformation. This is especially true of plant maintenance programs.
Although the food and beverage industry was certainly not alone in experiencing unprecedented operational challenges as a result of the pandemic. Organizations in nearly every facet of industry have, however for the food and beverage industry, these challenges such as fluctuating demand, increased safety regulations, exacerbated labor shortages and tightening budgets will require investing in new strategies in order to succeed.
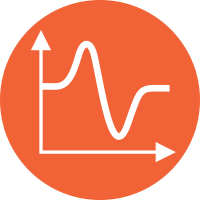
The food and beverage industry more so than other industries has been forced to adapt to unpredictable and fluctuating consumer demand.For example, the stress caused by the pandemic led Americans to consume more comfort foods. For the 52-week period ending September 6, 2020,ice cream sales were up 13 percent.
The pandemic has also given rise to new consumer preferences and behaviors such as online ordering and delivery services. And many consumers are still hesitant to return to restaurants even with restrictions being lifted and more people getting vaccinated.One survey conducted in March of 2021 found that nearly 25% of those surveyed will not feel comfortable eating indoors until herd immunity is reached.
The industry will continue to face complex supply and demand factors that will require the utilization of effective and strategic plant maintenance planning and scheduling in support of production operations.
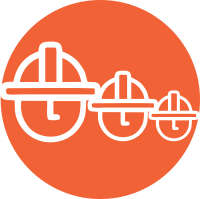
The food and beverage industry was already facing significant labor shortages before the pandemic. For instance, joint study conducted by Deloitte and The Manufacturing Institute Concluded that nearly 2.4 million manufacturing jobs were expected to go unfilled between 2018 and 2028. The growing labor shortage within the industry is due to several factors.
First, the industry is not appealing to younger generations.This is attributable to a significant public misconception about production and maintenance jobs. The industry is often viewed as archaic and failing to align with the importance that younger generations place on sustainability. Yet many food and beverage plants today utilize high-tech equipment and sustainable processes.As David Bryant,CEO of a Georgia-based consulting and recruitment firm summed it up several months before the COVID-19 outbreak, “The food and beverage industry has not done a good job publicizing itself as a fun, sexy job.”
Second, the Great Recession(2008-2009)resulted in massive job losses. An estimated one in five employees lost their jobs. This impacted all sectors of the food and beverage industry. Workers were forced to look for work in other fields. Many never returned. When the economy picked back up, organizations struggle with maintenance planning and finding experienced maintenance professionals. Or as Dan Crist, vice president of operations for A M Kingput it, “We have heard about labor shortage concerns from clients dating back to the Great Recession…Like many other industries, workers that were laid off during this period did not return to their jobs as the economy recovered.”
As bad as the Great Recession was, the unemployment rate rose higher three months into the pandemic than it did in two years during the Great Recession. Moreover, this economic downturn has coincided with the Baby Boomer generation reaching retirement age. Many skilled technicians are opting to retire and younger generations are not waiting in line to take their place.
And then there is the impact of the pandemic itself on the workforce. While more and more vaccinations are being administered, people are still getting sick. The possibility of prolonged worker absences and shortage poses ongoing operational and maintenance planning challenges.
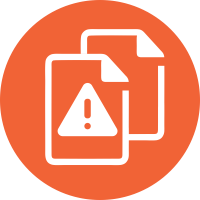
The food and beverage industry has always been subject to extensive safety and sanitation requirements. For instance, “FDA-regulated food manufacturers are required to follow Current Good Manufacturing Practices (CGMPs), have food safety plans, and implement preventative controls – all of which include requirements for maintaining clean and sanitized facilities and food contact surfaces.”
Yet COVID-19 ushered in a whole new set of regulations. For example, plants were required to reconfigure workspaces to provide for social distancing and limit the number of onsite workers. Moreover, additional sanitation measures were required, such as frequently disinfecting high-touch areas.Many of these regulations will become the new norm in the industry as plants have implemented them into their processes.
In the United States, the Food and Drug Administration (FDA) has continually published food safety updates throughout the pandemic. In August of 2020, the FDA and Occupational Safety and Health Administration (OSHA) released the “Employee Health and Food Safety Checklist for Human and Animal Food Operations During the COVID-19 Pandemic.” The checklist provides a quick reference guide for food manufacturers to comply with guidelines released by various governmental agencies. The first part of the guide provides extensive guidance on employee health and operation configuration. For example, the guidelines suggest the use of physical barriers, such as partitions, and keeping workers separated.
The second section highlights food safety requirements and directs manufacturers to consider the potential impacts that “personnel, suppliers, and incoming ingredients can have on their food safety or Hazard Analysis and Critical Control Points (HACCP) plan, as well as current good manufacturing practices (CGMPs).” Thus, the guidelines effectively extend beyond worker safety to potentially encompass a broad range of operational processes. Organizations will need to continue to monitor dynamic regulatory frameworks and be prepared to rapidly adapt operations as needed.
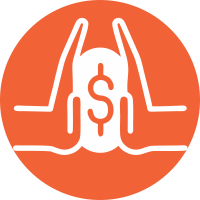
For the food and beverage industry, efficiency in operations is paramount.Margins are slim as many of their products are commodities and subject to intense price competition.Add to this the pandemic and resulting economic impact which had consumers looking to save as much money as possible. They did so by eating generic foods, making their own food, and not going out to eat. To make matters worse,the industry saw rising costs which could not always be passed on in the product price(which the consumer couldn’t afford).
From a maintenance standpoint,budgets were strained to sustain normal preventive maintenance tasks, nonetheless deal with an unplanned breakdown.According to a study conducted by Aberdeen Research, 82% of companies experienced unplanned downtime over a three-year period. These outages lasted an average of 4 hours and cost some $2 million.Food and beverage companies do not have the budgets to cover unplanned maintenance expenses. In addition, equipment downtime can result in perishable ingredients going to waste, production declines, and exacerbate the ability to meet customer demand resulting in lost profits.
The imperative for food and beverage companies today is to drive out costs and time waste to optimize operational efficiencies.
6 SAP Plant Maintenance Strategies
Organizations are increasingly turning to automation solutions to advance their preventive maintenance programs and optimize their plant maintenance planning and scheduling.The following are6 strategies for food and beverage companies with MAP reduce resource requirements and costs.
- Mobilize Maintenance to do More with Less
The growing labor shortage, accelerated by the pandemic, will persist. Maintenance professionals are reaching retirement age and retiring at record rates. Younger generations are not stepping in to fill the void. There are simply not enough experienced technicians to fill open plant maintenance positions, and there is limited budget to hire contractors.Therefore, organizations must optimize the use of their limited human resources by increasing wrench time.
According to McKinsey, “The average wrench time in the market is between 15 and 25%.Replacing paper-based work order processes with mobile devices(Mobile EAM) reduces administrative tasks and keeps maintenance technicians on the plant floor with the information they need at their fingertips for whatever maintenance task that is required – planned or unplanned. The result according to McKinsey can be significant, “we have seen companies increase wrench time 2.5x due to the digitization of maintenance processes.”
- Add automation toSAP Plant Maintenance Planning and Scheduling
With SAP, plant maintenance planning and scheduling processes are time-consuming. For example, downloading information, manipulating data in excel spreadsheets then manually inputting maintenance schedule back into SAP one-by-one.Add to this the inefficiency and costs of printing out and distributing work orders.Then, once the work is complete, the work order status must be manually inputted back into the system one-by-one. These manual data entry tasks lead to duplicate records, delayed and inaccurate data, and human error.
One way to automateSAP maintenance planning processes through a plant maintenance planning and scheduling solution for SAP. The solution makes it easy to download, organize and create schedules while maintaining data in SAP in a timely manner improving coordination between departments and keeping stakeholders informed.
- Go Beyond Preventive MaintenancePrograms
Many food and beverage plants rely on preventive maintenance processes.Preventive Maintenance aims to prevent major failures from occurring through a defined periodic maintenance plan.Reliability Centered Maintenance(RCM)takes preventive maintenance to the next level. For instance, by eliminating waste on tasks such as regularly replacing parts that fail randomly when they may have a much longer useful life. Or spending a lot of time fixing something that would cost less just to replace.For many assets,Predictive maintenance,can perfect preventive maintenance activities by leveraging data to predict and pre-empt equipment failure. Organizations experience far less downtime and far more effective technician usage.
Predictive maintenanceutilizesinformationfromsensorsandindustrial controls. Some examples of sensors include thermal imaging, vibration analysis, and temperature gauges. Many organizations have acquired the“smart”predictive maintenance technologies yet are challenged to use the information in their plant maintenance programs.Advancing SAP PM with a mobile solution to replace paper work orders,keeps data digitaland provides the means to easily integrate information from sensors and other sources into the technician’s workflows.
- Structure and Capture Data
To enable an RCM program and predictive maintenance activities, you need to make sure that you are collecting the right data. Maintenance professionals play a crucial role in the data collection processes. With a mobile solution, technicians can timely and accurately collect data and characterize the cause of failures. Replacing open text notes that can be difficult to analyze, mobile apps can include drop-down menus to help structure the data for analysis. Be sure to choose a mobile EAM solution that allows you to create custom, mandatory input fields to capture data for evaluation of failure modalities on your unique and critical assets.
Moreover, it is crucial to capture the knowledge of the older generations of maintenance professionals before they retire. These professionals possess intrinsic knowledge of industrial maintenance processes on your assets that will be incredibly valuable for new hires and contractors.
Keeping data digital through the end-to-end maintenance processes helps standardize, distribute,and improve the accuracy of information.
- Attract Younger Generations to Plant Maintenance Jobs
Even with powerful maintenance planning and scheduling solutions, technicians are needed to complete the work. The food and beverage industry must find ways of attracting younger generations to plant maintenance positions to fill vacancies left by retiring Baby Boomers.
Organizations should consider adopting technologies that younger generations are accustomed to using. For example, replacing paper-based processes with mobile devices. Or adopting Industry 4.0 technologies that younger generations are excited to work with, such as artificial intelligence (AI) and the Industrial Internet of Things (IIoT). With these younger tech-savvy maintenance professionals on board, they can help drive the organization to adopt and proactively use many of these new technologies which in the past were difficult and slow to introduce to the organization.
As organizations achieve digital transformation in their maintenance processes, the labor shortage should become less of an issue.
- Improve Operational Flexibility
The food and beverage industry as a whole was utterly unprepared for the pandemic. Organizations simply lacked emergency response and contingency plans because a global health crisis of this magnitude lacked precedent in modern times. And while we may not face a similar health crisis in our lifetimes, the pandemic has made clear the need to expect the unexpected and adapt quickly.
The need for flexibility is the main driving force behind the rapid acceleration in digital transformation initiatives. Cloud and digital technologies are inherently more scalable and adaptable allowing organizations to be more flexible. For the food and beverage industry, this includes incorporating changing safety regulations.
With the right technology investments, such as automating SAP plant maintenance planning and scheduling and going mobile, organizations can streamline and document their processes for greater efficiency and compliance.
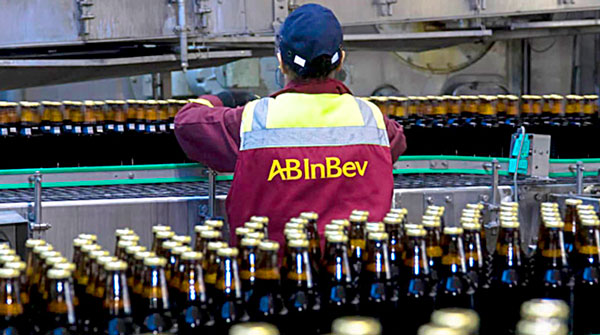
Real-world Results from the World’s Largest Brewer
Ambev Is part of Anheuser-Busch InBev, the largest brewing conglomerate in the world. Ambev chose Sigga’s Mobile EAM solution because it was the only solution that supported high-speed data synchronization between mobile devices and the SAP server.As a result, Ambev achieved significant results:
“Sigga Mobile EAM is the most complete maintenance and repair routine monitoring tool on the market, with very few competitors to date. I believe a lot in the application, in Sigga’s team and this is reflected in the internal acceptance of the solution.”
Robson Barbosa, Ambev Maintenance Engineer
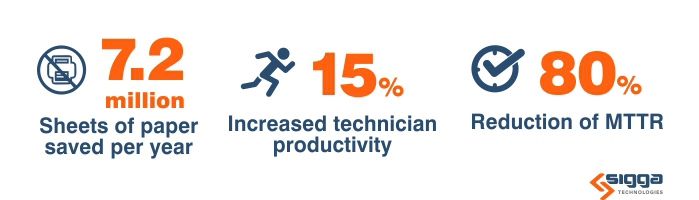
How Sigga Can Help
Sigga’s powerful digitization and mobile solutions have helped countless food and beverage organizations like Ambev to transform theirSAP plant maintenance processes.For 20 years, Sigga has honed customers’ SAP asset management and industrial maintenance processes withEAN productivity solutions.
Sigga’s Mobile EAM helps digitize SAP plant maintenance tasks and allows organizations to eliminate repetitive manual paper-based processes and increase maintenance productivity.
Sigga’s Planning and Scheduling Solution helps organizations to automate theirSAP plant maintenance planning processes. They can automatically check capacities, assign resources, prioritize work orders, track order status, and make informed decisions based on real-time data in SAP.